
State-of-the-art acrylic acid installation

When ECC-Prodecc wanted to further expand their acrylic acid installation, the Wilrijk-based company called on Agidens Fine Chemicals. Partly because of the current strict legislation concerning ATEX, Vlarem and CE, Agidens proposed a turnkey project for this: from risk analysis with associated HAZOP, conceptual design and drawing up the P&ID, all the way to E&I engineering and automation.
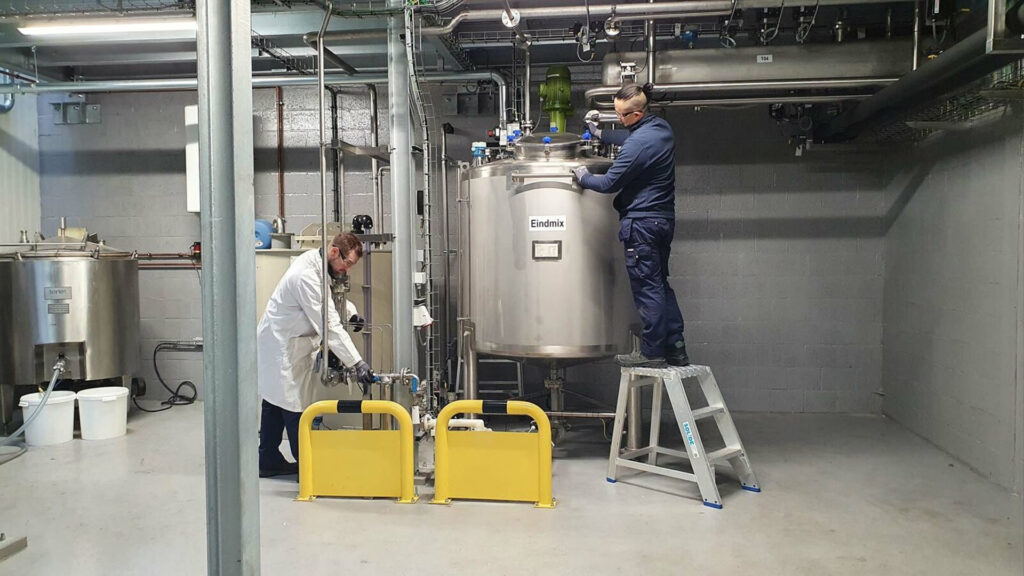
Mitigating Explosion Risks
Jonatan Cole, Senior Project Manager at Agidens Fine Chemicals: “Acrylic acid is a chemical product that has to be kept and processed at room temperature because of a risk of explosion at high temperatures. We therefore started up this project with a thorough risk analysis, including HAZOP, and we set out an ATEX zoning plan and explosion safety file. Because the new plant is to be built into a new space in the existing ECC-Prodecc buildings, we advised the external architect firm on the correct compartmentation of the ATEX zones and building-specific cooling and heating in the various production zones.
The new acrylic acid installation is composed namely of a storage tank for acrylic acid, three mix tanks, a pre-mix tank and final-mix tank, each time with their respective accessories and the necessary cleaning circuits. After delivery, Agidens is responsible for the service via a Service Level Agreement (SLA).
Turnkey project
Process Engineering
- P&ID
- Vlarem-compliant acrylic acid tank
- Batch process (ci. 5m³/u)
- Cycle times
Mechanical Engineering
Piping and diameters according to P&ID
E&I Engineering
- Drawing up I/O list
- Cable calculations according to EN60204
- Drawing up pneumatic dossier according to EN4414:2010
- Safety circuits according to EN-ISO-13849-1
Software Engineering
- Functional description based on process description
- Programming of PLC and HMI
Automation
The plant is controlled by a Siemens S7 PLC (in-built in a new control and power panel placed outside the ATEX zone) and is built as a stand-alone
Testing & Commissioning
- FAT: Results noted down in a handover report
- SAT: Functional testing of the components and functional testing of phases
“During our meetings with Agidens, we quickly realized that they have the necessary expertise in building plants for the manufacture of complex products such as ours. Agidens also offered an A to Z solution with the set-up and accompaniment of the project, always with the necessary aspects relating to Vlarem, ATEX and CE in mind. That gave us the peace of mind we needed to entrust the project to them. The next project we want to call on Agidens for is to revamp our old acrylic acid plant. That way, in time we will have two almost identical installations”.